
Tailor-made Colloidal Delivery
Systems® (CDS®)
Kol-Oil®
Designed to enhance extraction efficiency and well stimulation, Kol-Oil® harnesses CDS® nanotechology to boost oil production, optimise chemical treatments, and improve water-oil separation.
Slink-Oil®
Designed to enhance crude oil transportation and pipeline flow, Slink-Oil® harnesses CDS® nanotechology to reduce friction and viscosity, lower solvent use, and cut energy consumption.

Trusted by
industry leaders
CDS® has been benchmarked against major players like Halliburton, Schlumberger, and Baker Hughes—consistently delivering “best-in-class” results for oil recovery, treatment efficiency, and environmental stewardship. CDS® is an advanced nanotechnology built on over 25 years of R&D.



Why CDS® is a game-changer
Colloidal Nanotechnology
CDS® operates as a colloidal system composed of nanoscopic micelles—tiny globular structures that encapsulate, protect, and transport active ingredients (AIs). These micelles dynamically adapt their orientation based on the polarity of the AI (polar or non-polar) and the nature of the contact surface (e.g., rock, metal, oil, or water), ensuring optimal delivery and effectiveness.
Hydrophilic–Lipophilic Balance (HLB) Control
Engineered to span the full Hydrophilic–Lipophilic Balance (HLB) spectrum, CDS® can function in both water-based and oil-based environments. This allows it to seamlessly interface with and modify diverse media, making it ideal for use in complex reservoir formations and variable pipeline conditions.
Surface Modification & Chemical Activation
CDS® modifies the surface energy and interaction properties of reservoir rock and infrastructure materials, effectively reducing oil adhesion and improving flow. Acting as a chemical surface activator, it significantly increases the contact area for reactions—boosting the performance of treatment chemicals.
Controlled Delivery & Triggered Release
CDS® provides targeted delivery of active ingredients through its adaptive micellar structure:
-
It protects sensitive chemicals during transit.
-
It releases them precisely at the point of need, triggered by specific environmental conditions such as surface contact or chemical polarity shifts, following principles of chemical equilibrium.
Dose Rationalisation
By increasing the efficiency of active ingredients, CDS® allows for substantial reductions in chemical dosing—typically only 30–50 parts per million (ppm) are required. This results in lower operational costs, reduced environmental impact, and minimised residual waste.
Reduces Active Ingredient Doses
30-40%
Improves Through-
put Productivity
22% - 25%
Generates Net Savings & Lifts Profit
18% - 20%
Certified Organic & Eco-Friendly
100%
Advantages for oil producers
Boosts Heavy
Crude Flow
-
Reduces oil viscosity for easier extraction and transport
-
Alters rock surface properties to lower oil adhesion
-
Enhances fluid penetration and waterflood efficiency
-
Prevents wax deposition in pipelines
Revives Mature
& Dead Wells
-
Improves oil mobility, unlocking previously trapped hydrocarbons
-
Enables enhanced oil recovery (C-EOR®) from low-performing wells
Improves Chemical
Treatment Efficiency
-
Increases contact area between chemicals and reservoir rock
-
Delivers multiple active ingredients effectively, even incompatible ones
-
Reduces required dosages of treatment chemicals by 30-40%
Helps Prevent
Corrosion
-
Generates a nanobarrier or gradient interfacial film on crude oil to minimise metal surface interaction and suppress corrosive reactions
-
Enhances corrosion inhibitor effectiveness and controls release rate
Helps Reduce
Scale Formation
-
Disperses scale-forming minerals and wax crystals
-
Inhibits crystal growth and adhesion to pipe walls
-
Improves scale inhibitor performance with controlled release
Minimises
Environmental Impact
-
Produced from natural materials—safe for people, pipelines, and the planet
-
A powerful ESG enhancer that lowers emissions, chemical footprints, and waste output
Advantages for refineries
Optimises Desalting
& Treatment Processes
-
Reduces desalting time dramatically (from days to hours)
-
Decreases operating temperatures, improving thermal efficiency
Reduces Energy Consumption
-
Lowers fuel use in heating operations by up to 80%
-
Enhances heat transfer and allows effective treatment at lower temps
Expands Fluid Treatment Capacity
-
Increases capacity by up to 40% without physical infrastructure expansion
-
Reduces residence time and improves throughput
Minimises Environmental Impact
-
Produced from natural materials—safe for people, pipelines, and the planet
-
A powerful ESG enhancer that lowers emissions, chemical footprints, and waste output
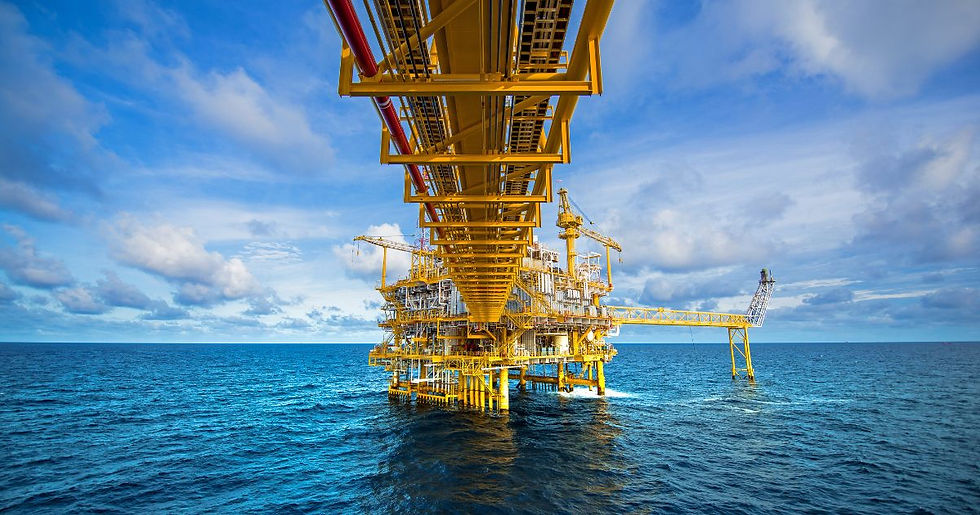
Recent posts
